Faq Help Center
The very high quality of materials and components together with high performance in terms of reliability and wear resistance guarantee to our products excellent performances in every industrial area.
Why Plunger Pump
Plunger pumps are a special version of piston pumps in which the reciprocating action of ceramic plungers allows fluids to go through check valves in and out of a pressure chamber. The plunger is normally made out of hard ceramic, which is very durable and resistant. Plunger pumps can be used in many industrial applications, such as process technology in the chemical industrial or cleaning applications.
Plunger pumps use the reciprocating action of ceramic plungers to pressurize fluids and force them through outlet valves. The plunger is generally made out of durable and particularly resistant hard ceramic. In plunger pumps the plunger is attached to a rotor with a connecting rod so, when the ceramic plunger reciprocates out, it produces suction pressure. As the rotor turns, the plunger is pushed back down to send fluid through the outflow valve. One of the advantages of plunger pumps is that they can be used at much higher pressures than piston pumps.
Plunger pumps are oscillating positive displacement pumps in which the displacers (called “plunger”) are moved by crankshafts which are integral to the pump. The action of ceramic plungers allows fluid to go through check valves in and out of a pressure chamber. Plunger pumps can be used in a wide range of applications (such as high-pressure cleaning, misting and cooling systems or vehicles cleanings) and have many advantages:
- plunger pumps can be adapted to pump various fluids (also abrasive, corrosive, toxic and flammable fluids) even under high pressures
- if the driving motor is strong enough, they can be used in processes with highest pressures
- due to the design, plunger pumps work with the maximum efficiency and allow to save energy
- easy installation
Plunger pumps can be used in a wide range of applications, such as high-pressure cleaning or vehicle cleaning. In particular, plunger pumps ensure maximum efficiency, reliability and resistance even under stressful conditions and are suitable for:
- car-wash
- pressure washing
- water jetting systems
- fire-fighting systems
- drilling industry
- road sweepers and washers
- orchard and vineyard spraying
- sewer-jetting
Cant find an answer? ask us
Applications
Ecological intervention that makes the places sanitized. It is a technique that uses high pressure water to remove the layer of dirt on ground surfaces of the walls, facades and fences.
The car wash is a high pressure water system, with the addition of chemical detergents and osmotic water used to clean the exterior and, in some cases, the interior of motor vehicles. The plant can be self-service, fully automated or equipped with personnel for vehicle wash.
All items that come into contact with food must be effectively cleaned and disinfected. This is a process that removes food waste, dirt, grease and destroys foodborne disease pathogens.
The truck wash is a high pressure water system, with the addition of chemical detergents and osmotic water used to clean the exterior and, in some cases, the interior of motor vehicles. The plant is fully automated or equipped with personnel to wash the vehicle.
The technology consists of spraying water at high pressure through spray nozzles with a calibrated hole so that the size of the sprayed water droplets create the size of the suspended particles.
Reverse osmosis, also called hyperfiltration, is the process in which the passage of water is forced from the more concentrated solution to the less concentrated solution obtained by applying a higher pressure than the osmotic pressure to the more concentrated solution
Controlled Horizontal Drilling also known as directional drilling, controlled horizontal drilling or remote controlled drilling, is a no dig technology suitable for the installation of new pipelines without carrying out open pit excavations.
Heat exchangers are used day by day all over the world not only for chemical and thermal processes and in Oil Gas, but also for their reverse application, air conditioning units. Since heat exchangers are such an important part of the operation of many businesses, it is important to keep them clean and operating to their full potential.
A street sweeper is a machine that cleans the streets. The use of high pressure water keeps dust under control.
The mist irrigation system is one of the gravity irrigation systems (together with the submersion, flow irrigation, and lateral infiltration systems). It takes place by small sprinklers that atomize high pressure water.
A fire extinguishing system uses a very fine mist of water as an extinguishing agent. The micro-droplets allow the control, suppression and extinction of the flames.
Misting is a phenomenon caused by small droplets of water suspended in the air. Physically, it is an example of dispersion. It is most commonly seen where warm, humid air encounters sudden cooling. It can be artificially created with dedicated systems using high pressure water and a dedicated nozzle network.
Use & maintenance
The viscosity rating is very important for identifying whether an oil is suitable for specific operating conditions: oils with a high viscosity rating are ideal for use in summer, whereas oils with lower viscosity ratings are best in winter. Multi grade oils are capable of adapting and their operating range is described by two numbers: the cold temperature viscosity and the hot temperature viscosity. Leuco S.p.A. recommends using SAE 10W-40 multi grade oils with its pumps.
The code for multi grade oils consists of two numbers separated by a “W”: the first number shows the low temperature rating and the second number is the high temperature rating. Multi grade oils help cold starts: their fluidity at low temperatures facilitates cold starts and safeguards the lubricating film even during the critical pump start-up phase.
The maximum hot temperature is 100°C. This temperature was originally chosen to represent the oil temperature and is still used to define SAE ratings. However, developments in engine technology mean that oil temperatures can now reach significantly higher values (150°C or more).
The pumps can use either mineral or synthetic oils!
High-pressure piston pumps are positive displacement pumps. The main parameters that determine your choice of Hawk pump are flow rate, pressure, rotation speed and power consumption.
The flow rate is given in litres per minute and is directly proportional to the speed of rotation.
The speed of rotation is given as revolutions per minute.
The pressure is given in bars and is the maximum pressure that the pump was designed to reach.
The power consumption is shown in kW and is the absorption required to achieve the maximum flow rate and pressure indicated.
Among the pumps, HAWK proposes:
Standard Pumps, suitable for the majority of applications that need to pump clean fresh water or water with a low percentage of commonly used detergents, up to a temperature of 65 °C.
Aisi 316l Stainless Steel Manifold Housing Pumps, suitable for applications involving reverse osmosis, for use in the food- chemical and pharmaceutical industries and for applications using seawater.
Car Wash Pumps, which have a special seals pack designed for the car wash sector in order to ensure longer seal life, low maintenance and reliable car wash operation with no downtime. Anti-corrosion nickel plated manifold housing offering superior protection even in the most challenging conditions.
Ht Pumps, which have a special seals pack designed for the food industry and for all applications up to 85°C to prevent problems often associated with the use of hot water. Anti-corrosion nickel plated manifold housing offering superior protection even in the most challenging conditions.
Atex Pumps Category II 2G c T135°C (T4), atex certified pumps, which can be integrated in appliances operating in potentially explosive environments.
We are often asked what is the difference between a pressure control valve and an unloader valve. The main function of pressure control valves is to set and maintain constant pressure in the system, acting as the main device for releasing pressure. These valves are used in systems where a continuous outlet flow is required for the whole time the pump is running. It is essential to fit an unloader valve in systems where outlet flow is not required from the nozzle even when the pump is running. This type of valve has the main function of a pressure control
valve but it contains a releasing device that redirects the flow through a by-pass line when the outlet on the nozzle is closed (for example via a gun). The by-pass flow can be connected to the source of the system or drained off. When connecting the by-pass to the source, a thermal valve must be fitted for protection against overheating. In this type of system, if there were no way to release the pressure through the by-pass pipe line, there would be an increase in pressure that could endanger the system.
To prevent damage to the pump or injury, it is essential to fit a pressure control valve and a safety valve to prevent the pressure accidentally exceeding its operating value. Contact your dealer to be sure of choosing the best valves for your application.
The pump should not be used at higher pressures or speeds of rotation than those described for each product version in this manual.
The pump should be installed horizontally with respect to its base to facilitate optimum lubrication.
The pump’s suction line must be proportional to the flow rate and its diameter must not be less than the diameter of the suction mouth. It is important that there be as few bottlenecks on this
line as possible (elbows, T couplings, reductions, etc …). Each junction on the suction line must be sealed properly with Teflon tape or a similar product to avoid leaks or air intake (cavitation).
Fit a filter to capture any impurities.
Before starting up the pump, make sure the oil is up to level. We recommend the first oil change within the first 50 hours of operation. Subsequent oil changes should take place every 500
hours, or more often in case of heavy use. Use the oil indicated on the pump’s specifications label.
After starting up the pump, aid priming by keeping the delivery line open. Do not let the pump run dry: this can result in rapid seal wear and invalidates the warranty.
When using chemicals, run the pump with clean water for several minutes after use. Do not use the pump at very low temperatures. To prevent freezing, run the pump dry for about 20 seconds to drain the pipes.
If the pump has been inactive for a long time, a small amount of water may leak from the seals for the first few minutes of operation.
CHEMICALS
It is possible to use certain chemical cleaning products. The cleaning product can be added upstream (delivery – high pressure) or downstream (suction – low pressure) to the pump.
Analyse the chemical before use to ensure it is compatible with the materials of the system parts.
You must comply with legal standards for the protection of the environment when using chemicals.
Chemicals can always be added by means of a venturi. A small venturi is sufficient as there is high pressure downstream to the pump; a larger mixer will be required upstream to the pump.
Using an injector downstream to the pump has several benefits.
- Less exposure of components to the chemicals.
- Using the injector downstream is more cost effective as it runs on low pressure.
- The machine operator can control the flow of the chemical more easily by changing the aperture of the venturi on the lance.
Generally, the injectors downstream are double lances and usually need an operating pressure of circa 50 bar.
Oversized injectors can lead to a strong drop in pressure and a higher concentration of chemical being added. Vice versa, the chemical will not be mixed properly if the injector is too small.
If you opt to pass the chemical through the pump, it will be subject to corrosion due to the effects of the chemical itself. Only opt for mixing on the suction line if the chemical is mild. If this is not the case, choose a high pressure mixer, possibly upstream to the nozzle, so that practically no components are affected by the corrosive effects of the chemical.
The pH must be between 5 and 9. A filter must be fitted with a pore size of 20÷30 µm if the water contains abrasive particles.
HIGH TEMPERATURE
Hot water can be used instead of chemicals or in addition to them. Again, you can choose to pump hot water directly or to heat it downstream to the pump.
Always check that parts can tolerate the operating temperature.
High temperatures reduce the life of system parts, especially the seals and the automatic check valves in the pump as well as parts for closing and sealing in the control and safety valves and in the gun. Another result is rapid nozzle wear.
Manufacturer guarantees pump products from defects in their construction and materials for a period of 1 year from the time they leave the factory. This guarantee is limited to the repair and replacement of parts or products that Manufacturer deems were defective at the time of delivery. All the products covered by this limited guarantee must be returned freight paid for inspection, repair or replacement by the manufacturer. This limited warranty is the only form of valid guarantee and replaces any other form of explicit or implicit warranty, including guarantees of fitness for sale or any particular purpose. The manufacturer refuses any such liability with this statement.
Faulty products will only be repaired or replaced according to these terms. Manufacturer is not liable for any further loss, damage or expense including accidental or indirect damages caused directly or indirectly from the sale or use of these products.
The unauthorised use of spare parts that were not manufactured by Manufacturer automatically invalidates this guarantee, which is subject to compliance with the instructions for installation and operation provided.
There are no additional guarantees other than the guarantee described above.
Manufacturer does not recognise any guarantee on standard consumables, such as seals, valves, housings, or orings.
This guarantee does not cover and Manufacturer is not liable in case of faults or failures due to incorrect or lack of maintenance, incorrect lubrication due to an incorrect level of oil in the crankcase, pumped liquids below pH 5 or above pH 9, above 500 cps, general wear and damage, damage or wear caused by incorrect installation, incorrect use, improper use, accidents, excessive abrasion, corrosion, frost or heat, tampering, replacement of the original
parts.
This guarantee does not cover and Manufacturer is not liable in case of malfunction, damage or wear caused by the incompatibility of the product with the structure, accessories, products or materials not supplied by Manufacturer.
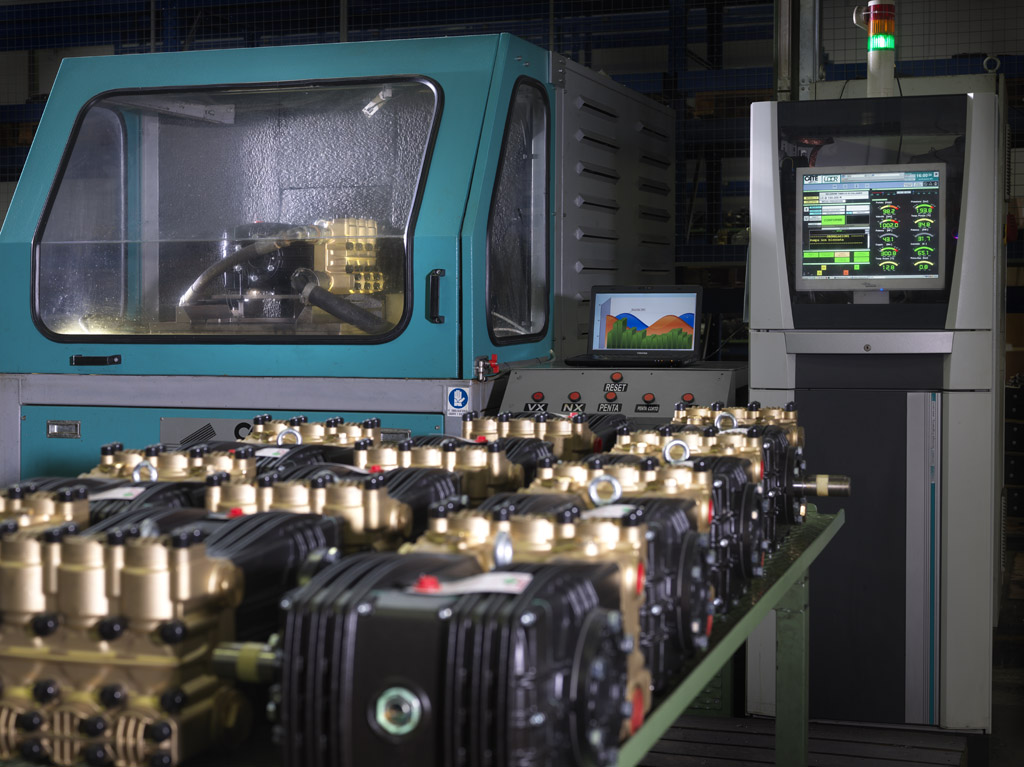